Tech Theory: Technical…Practical… Interesting Automation Industrial Solutions
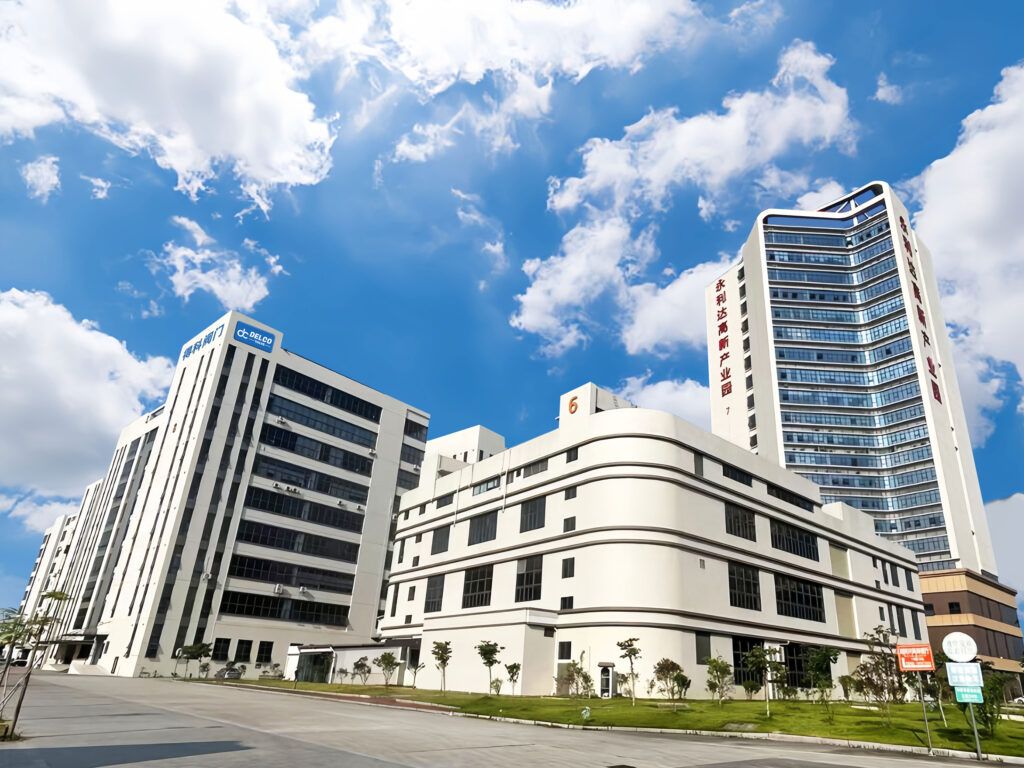
At DELCO, we understand the importance of customer satisfaction and strive to meet the unique needs of every client. As a reliable valve supplier, we are committed to providing excellent customer service and high-quality products to ensure optimal performance and longevity. By choosing DELCO as your trusted control air supplier, you can benefit from customized valve assemblies designed specifically to meet your requirements, enhancing efficiency and reducing downtime.
Summary and Solutions to Common Malfunctions of Pneumatic Control Valves
The common faults of pneumatic control valves are summarized as follows:
(1) The regulating valve does not operate, and the fault symptoms and reasons are as follows:;
1. No signal, no gas source. 1. The gas source is not turned on. 2. Due to the water content in the gas source, it freezes in winter, causing blockage of the air duct or failure of the filter and pressure reducing valve. 3. Compressor failure. 4. Leakage of the gas source main pipe.
2. There is a gas source but no signal. 1. Regulator malfunction 2. Positioner corrugated steel leakage 3. Damaged regulating mesh plate
3. The locator has no air source, 1. The filter is blocked, 2. The pressure reducing valve is faulty, and 3. The pipeline is leaking or blocked
4. The locator has a gas source but no output. The throttle hole of the locator is blocked
5. There is a signal but no action. 1. Valve core detachment, 2. Valve core jamming with society or valve seat, 3. Valve stem bending or breaking, 4. Valve seat valve core freezing or coking debris. 5. The actuator spring died due to long-term disuse.
(2) The action of the regulating valve is unstable. The fault symptoms and causes are as follows:
1. Unstable gas source pressure 1. Compressor capacity too small 2. Pressure reducing valve malfunction
2. Unstable signal pressure 1. Inappropriate time constant of the control system 2. Unstable output of the regulator
3. The gas source pressure is stable, and the signal pressure is also stable, but the action of the regulating valve is unstable. When the ball valve of the amplifier in the locator is not tightly worn by dirt and the gas consumption increases significantly, it will produce output oscillation. 2. The nozzle baffle of the amplifier in the locator is not parallel, and the baffle cannot cover the nozzle. 3. The output pipe and line are leaking air. The rigidity of the actuator is too low. The friction resistance is high during the movement of the valve stem, and there is obstruction at the contact area.
(3) Adjust valve vibration. The fault symptoms and causes are as follows:
1. The regulating valve vibrates at any opening. 1. Unstable support 2. There are vibration sources nearby 3. The valve core and liner are severely worn.
2. The regulating valve vibrates when in the fully closed position. 1. The regulating valve is selected too large and is often used at a small opening. 2. The medium flow direction of the single seat valve is opposite to the closing direction
(4) The phenomenon and reasons for the sluggish action of the regulating valve are as follows:
1. The valve stem only moves slowly in one direction. 1. The diaphragm in the pneumatic diaphragm actuator is damaged and leaks. 2. The “O” seal in the actuator leaks
2. The valve stem is sluggish during reciprocating motion. 1. There is adhesive blockage inside the valve body. 2. The PTFE packing has deteriorated and hardened, or the graphite asbestos packing lubricating oil has dried Adding 3 fillers too tightly increases frictional resistance. Due to the non straight valve stem, there is high frictional resistance. Pneumatic control valves without locators can also cause sluggishness
(5) The leakage of the regulating valve increases, and the reasons for the leakage are as follows
1. When the valve is fully closed, there is a large amount of leakage. 1. The valve core is worn and the internal leakage is severe. 2. The valve is not properly adjusted and cannot be tightly closed
2. The valve cannot reach the fully closed position. 1. The medium pressure difference is too large, the rigidity of the actuator is small, and the valve cannot be tightly closed. 2. There are foreign objects inside the valve. 3. The lining is sintered
(6) The adjustable range of traffic becomes smaller. The main reason is that the valve core is corroded and becomes smaller, thereby increasing the adjustable minimum flow rate.
Understanding the faults and causes of pneumatic control valves can enable targeted measures to be taken to solve them.
At DELCO, we understand the importance of customer satisfaction and strive to meet the unique needs of every client. As a reliable control valve supplier, we are committed to providing excellent customer service and high-quality products to ensure optimal performance and longevity. By choosing DELCO as your trusted control valve supplier, you can benefit from customized valve assemblies designed specifically to meet your requirements, enhancing efficiency and reducing downtime.
Furthermore, our competitive pricing on electronic pressure regulators enables you to offer top-notch solutions. As one of the leading control valve manufacturers, we take pride in delivering reliable valves that not only meet industry standards but also contribute to the overall profitability of your business. By partnering with DELCO, you can have peace of mind knowing that you are making a wise choice for the long-term success of your company.