Tech Theory: Technical…Practical… Interesting Automation Industrial Solutions

At DELCO, we understand the importance of customer satisfaction and strive to meet the unique needs of every client. As a reliable valve supplier, we are committed to providing excellent customer service and high-quality products to ensure optimal performance and longevity. By choosing DELCO as your trusted control air supplier, you can benefit from customized valve assemblies designed specifically to meet your requirements, enhancing efficiency and reducing downtime.
Principles, Types, and Applications of Control Valves
Control valves play a crucial role in industrial processes and are widely used in petroleum, chemical, power, and metallurgy industries. This article will explore the principles, types, and applications of control valves in various fields.
Table of contents
1. Basic Principles of Control Valves
A control valve is a device that can regulate fluid flow by varying its opening degree to control parameters such as flow rate, pressure, and temperature within a pipeline. A control valve primarily consists of an actuator and a valve body.
1.1 Actuator
The actuator is the driving device of the control valve, receiving signals from the controller and converting them into mechanical movements to adjust the valve opening. Depending on the driving method, control valves can be categorized into pneumatic, electric, and hydraulic types:
- Pneumatic Actuator: Driven by compressed air, known for its quick response and high control accuracy.
- Electric Actuator: Driven by an electric motor, suitable for remote control applications with simple operation and a high degree of automation.
- Hydraulic Actuator: Driven by hydraulic fluid, ideal for high-pressure and large-diameter control valves.
1.2 Valve Body
The valve body is the main component of the control valve that directly contacts the fluid, determining the valve’s flow capacity and control characteristics. Common types of valve bodies include ball valves, butterfly valves, gate valves, globe valves, and diaphragm valves.
2. Types of Control Valves
Control valves can be classified into various types based on their functions and structures. Here are some common types of control valves and their characteristics:
Ball valves use a rotating ball to open and close the valve, providing full-open and full-close functionality. They are known for good sealing, simple structure, and low flow resistance, making them suitable for quick shutoff and frequent operation. However, ball valves have poor regulating performance and are not suitable for precise flow control.
Butterfly valves adjust fluid flow by rotating a disc. They feature a simple structure, lightweight design, and low cost, making them suitable for flow control in large-diameter pipelines, commonly used in water treatment and HVAC systems. However, butterfly valves have poor sealing performance and are not suitable for high-pressure, high-temperature media.
Gate valves control fluid flow by lifting a gate. They offer low flow resistance and good sealing performance, suitable for fully open or fully closed applications. Gate valves are commonly used in oil and gas pipelines.
Globe valves adjust flow by lifting a plug. They offer good regulating performance and high sealing capability, suitable for applications requiring precise flow control. However, they have high flow resistance and are best suited for smaller diameter pipelines.
2.5 Diaphragm Valves
Diaphragm valves achieve opening and closing through a flexible diaphragm, making them suitable for controlling media with solid particles or corrosive properties. They are known for being leak-free and having a simple structure, widely used in the chemical and pharmaceutical industries.
3. Applications of Control Valves
Control valves are widely used in industrial production, with several key application areas:
3.1 Oil and Gas Industry
In the oil and gas industry, control valves are used to regulate the extraction, transportation, and processing of oil and gas. For example, during oil well extraction, control valves regulate the production rate, ensuring safe and efficient operation. In transportation pipelines, control valves adjust the flow rate and pressure of oil and gas to prevent overpressure or leaks.
3.2 Chemical Industry
In the chemical industry, control valves control various process parameters such as temperature, pressure, and flow rate in chemical reactions. For example, in chemical reactors, control valves regulate the feed rate of reactants, control reaction temperature and pressure, ensuring optimal reaction conditions. Additionally, control valves play a key role in distillation, drying, and cooling processes in chemical production.
3.3 Power Industry
In the power industry, control valves are used in steam systems of thermal power plants and nuclear power plants. For example, in boiler systems, control valves regulate the flow rates of fuel, air, and water to ensure efficient boiler operation. In turbine systems, control valves adjust steam flow and pressure to ensure stable turbine operation and power generation efficiency.
3.4 Water Treatment Industry
In the water treatment industry, control valves are used in water transportation, filtration, disinfection, and other processes. For example, in water treatment plants, control valves regulate water flow and pressure to ensure normal operation of the water supply system. In wastewater treatment plants, control valves adjust the flow rate and various parameters during the treatment process to meet discharge standards.
3.5 Pharmaceutical Industry
The pharmaceutical industry requires high standards for production environments and process control, where control valves play a crucial role. For instance, during pharmaceutical production, control valves regulate the feed of reactants, the addition of solvents, reaction temperature, and pressure to ensure product quality and production efficiency. Additionally, control valves are essential in the cleaning and sterilization processes of pharmaceutical equipment.
4. Selection and Maintenance of Control Valves
4.1 Selection of Control Valves
Choosing the right control valve is critical for the safety and efficiency of industrial production. Several factors need to be considered during selection:
- Medium Characteristics: Different media require different materials and structures for control valves, such as corrosion-resistant materials for corrosive media.
- Operating Parameters: The operating pressure, temperature, and flow rate of the control valve need to match the actual working conditions.
- Control Requirements: Select the appropriate actuator and valve body structure based on control accuracy and response speed requirements.
- Installation Conditions: Consider the installation position and environmental conditions of the control valve, such as space constraints and ambient temperature.
4.2 Maintenance of Control Valves
Regular maintenance is essential to ensure the normal operation of control valves, focusing on the following aspects:
- Check Sealing Performance: Regularly check the sealing surfaces of the control valve to prevent leakage.
- Clean Valve Body and Pipeline: Regularly clean the valve body and pipeline to prevent blockages caused by impurities in the medium.
- Lubricate Actuators: Regularly lubricate pneumatic and electric actuators to ensure their flexibility and reliability.
- Calibration and Adjustment: Regularly calibrate and adjust control valves to ensure their control accuracy and response speed.
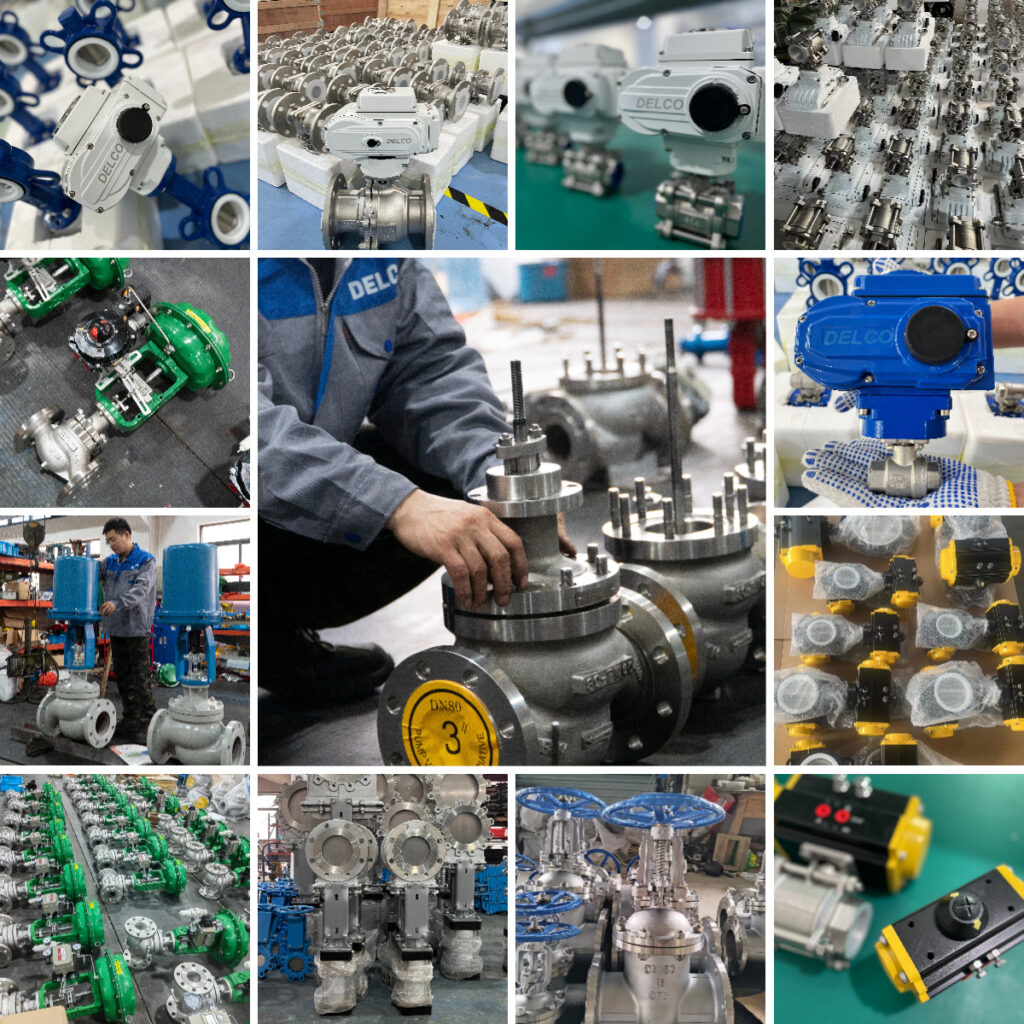
5. Trends in Control Valve Development
With the advancement of industrial automation and intelligence, control valves are continuously innovating and evolving. Future trends in control valve development include:
5.1 Intelligence
Intelligent control valves equipped with sensors, actuators, and control units can monitor and feedback operating status in real-time, enabling remote monitoring and diagnostics, thus improving production efficiency and safety.
5.2 High-Performance Materials
The application of new materials enhances the reliability and lifespan of control valves in high-temperature, high-pressure, and corrosive environments. For example, ceramic materials and special alloys are increasingly used in control valves.
5.3 Environmental Protection and Energy Saving
The design and manufacturing of control valves are more focused on environmental protection and energy-saving, such as low-energy consumption actuators and leak-proof designs, promoting green industrial production.
5.4 Customization
The customization level of control valves is increasing to meet the needs of various special working conditions. For instance, controlling special fluids and achieving high-precision regulation.
6. Conclusion
Control valves, as critical equipment in industrial process control, have complex principles, types, and applications. Through a deep understanding and scientific selection of control valves, the safety, stability, and efficiency of production processes can be effectively enhanced. With the continuous development of technology, control valves are innovating and advancing towards intelligence, high performance, environmental protection, and customization. In the future, control valves will play an essential role in more fields, contributing to the development of industrial automation and intelligence.
7. How to get a quick quote for industrial valves?
If you have questions about valves or want to get a quote, please feel free to contact us, we will reply within 6 hours. Phone +86 150 1535 8097, WhatsApp +86 150 1535 8097 or email marketing [email protected].
DELCO’s quality, competitive prices and excellent service make it the best valve partner to help you grow your business. Customize your valves, we have no minimum order.
At DELCO, we understand the importance of customer satisfaction and strive to meet the unique needs of every client. As a reliable control valve supplier, we are committed to providing excellent customer service and high-quality products to ensure optimal performance and longevity. By choosing DELCO as your trusted control valve supplier, you can benefit from customized valve assemblies designed specifically to meet your requirements, enhancing efficiency and reducing downtime.
Furthermore, our competitive pricing on electronic pressure regulators enables you to offer top-notch solutions. As one of the leading control valve manufacturers, we take pride in delivering reliable valves that not only meet industry standards but also contribute to the overall profitability of your business. By partnering with DELCO, you can have peace of mind knowing that you are making a wise choice for the long-term success of your company.