Tech Theory: Technical…Practical… Interesting Automation Industrial Solutions

At DELCO, we understand the importance of customer satisfaction and strive to meet the unique needs of every client. As a reliable valve supplier, we are committed to providing excellent customer service and high-quality products to ensure optimal performance and longevity. By choosing DELCO as your trusted control air supplier, you can benefit from customized valve assemblies designed specifically to meet your requirements, enhancing efficiency and reducing downtime.
Control Valve Overview and Selection Guide
Control valves play a key role in regulating fluid flow in industrial processes. By adjusting the opening of a valve, we are able to precisely control the flow of liquids, gases or vapors to meet the process requirements. In this article, we would like to systematically and professionally introduce different types of control valves, components, functions, application scenarios and valve accessories.
Table of contents
- Basic Introduction to Control Valves
- What is a control valve?
- How control loops work.
- Types of control valves
- Control valve components
- Accessories
- Typical applications of valves
- Understand the most appropriate type of flow control valve for your application
- Basic Control Valve Terms and Explanations
- Why more and more international valve brands choose DELCO for OEM service?
- How to get a quick quote for industrial valves?
Basic Introduction to Control Valves
In this section, we will provide a brief introduction to the control valve to assist you in understanding its definition and its function in the system.
Control valve is a key device used to regulate the flow of fluid, by changing the opening of the valve, to achieve precise control of the fluid in the pipeline. It plays a vital role in industrial process control systems and can be used to regulate parameters such as temperature, pressure, and liquid level to ensure stable system operation.
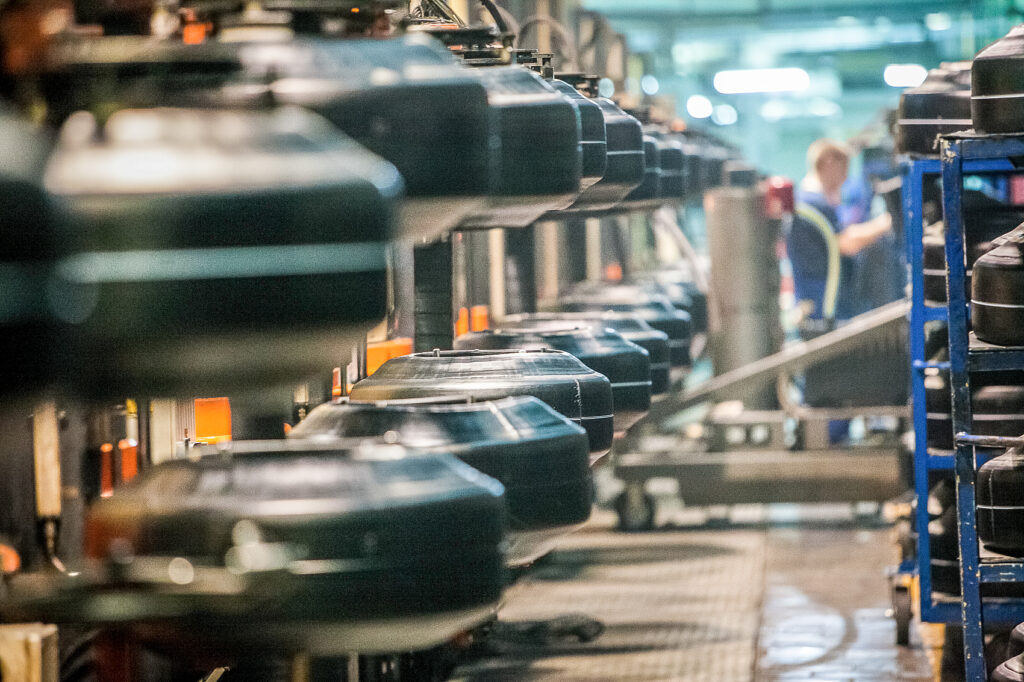
How control loops work.
Control loops work by sensing variables in the system, comparing them to preset values, and then using control valves to adjust the fluid flow to bring the system to a desired state. This adjustment process can be accomplished through feedback control, feed-forward control, or a combination of both, ensuring that the system responds quickly and accurately to changes.
Types of control valves
There are various types of control valves, which are mainly classified into the following categories according to their design and application:
Shut-off valves:
This valve is usually used to regulate the flow of fluids. It has a conical or spherical flap and can be operated manually or automatically to adjust the degree of opening and closing of the valve.
Plug Valve:
Because of their simple construction and operation, plug valves are usually used in applications requiring rapid opening and closing. The valve flap resembles a rotating disk that is rotated to control the passage of fluid.
Ball Valves:
A ball valve uses a rotating sphere to control the flow of fluid. It is characterized by rapid opening and closing and is usually used in systems where rapid shutoff of fluid is required.
Regulating Valves:
These valves are specifically designed to precisely regulate the flow, pressure, or temperature of a fluid. Regulating valves are usually equipped with controls that dynamically adjust the position of the valve according to system requirements.
Butterfly Valves:
Butterfly valves are used to prevent backflow of fluid and have a flap that allows fluid to pass in one direction. This type of valve is usually used in systems where backflow prevention is required.
Motorized Valves:
This is a class of valves that are controlled by an electric motor or solenoid mechanism and can be operated remotely or automatically. Motorized valves are usually used in systems requiring a high degree of automation.
These are just some of the common types of control valves, in fact there are other specially designed valves to suit different industrial applications and fluid control needs.
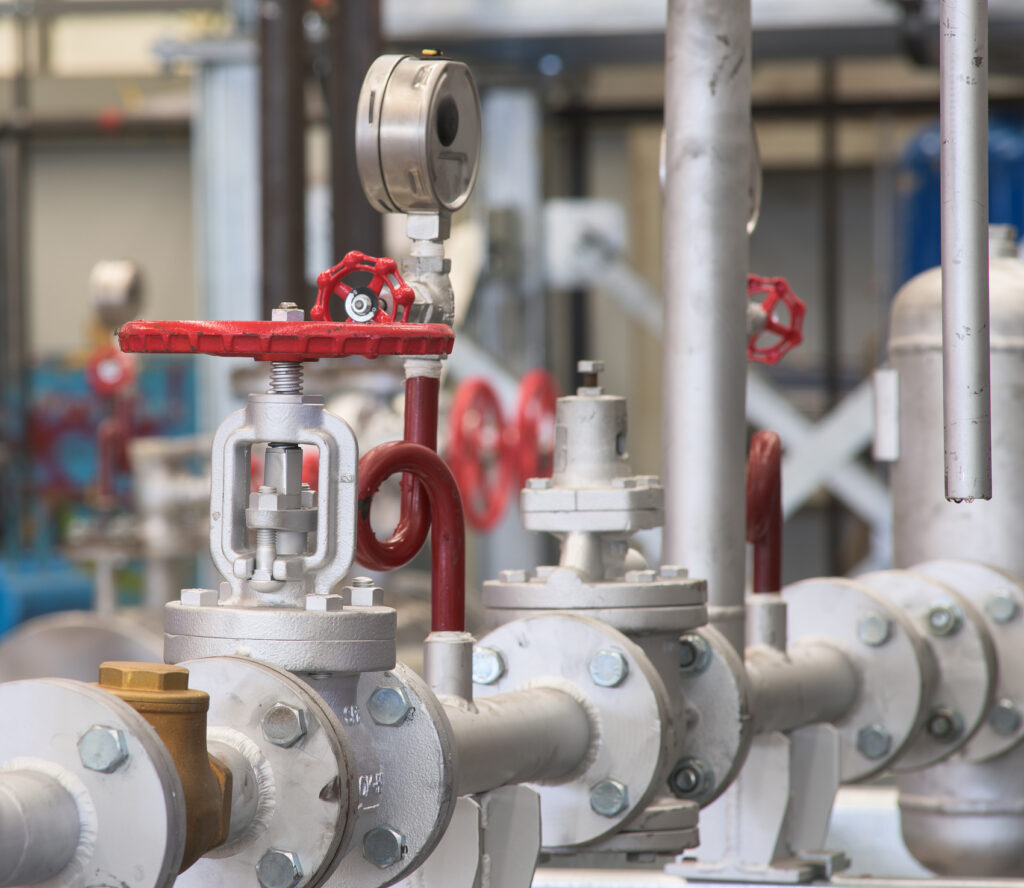
Control valve components
Control valves typically consist of several key components that work together to achieve precise control of fluid flow, pressure, or temperature. The following are some common control valve components:
Valve Body:
The valve body is the main enclosure of the control valve, which contains the valve and other key components. The shape and construction of the valve body depends on the type and purpose of the valve.
Valve:
Valve is the moving part of the control valve which regulates the on-off or flow of fluid by rotating, lifting or swinging. The design of valves varies according to the type of valve.
Valve Seat:
The seat is the fixed part of the valve that fits into the valve when it is closed and ensures that the valve is completely sealed. A good seal is critical to the proper operation of the valve.
Valve stem:
The stem is the part that connects the valve to the control device (e.g., actuator) and is responsible for transmitting the motion of the actuator to the valve to open and close the valve.
Actuator:
The actuator is the power part of the control valve, which drives the movement of the valve according to the input of external signals (manual, electric, pneumatic or hydraulic). Types of actuators include electric actuators, pneumatic actuators, etc.
Position feedback device:
The position feedback device is used to measure the actual position of the valve and transmit the feedback signal to the control system to ensure that the valve reaches the predetermined position for precise fluid control.
Valve cover:
The bonnet is the top part of the valve body and usually contains the stem seal. It ensures that the valve does not leak during operation.
Seal:
Seals are used to prevent fluid leakage when the valve is closed. They are usually located between the seat, valve and bonnet.
The combination and synergy of these components allow control valves to reliably perform fluid control tasks in industrial processes. Different types of control valves may have different component configurations and operating principles.
Accessories
Control valve fittings can vary depending on specific applications and needs, but the following are some common control valve fittings:
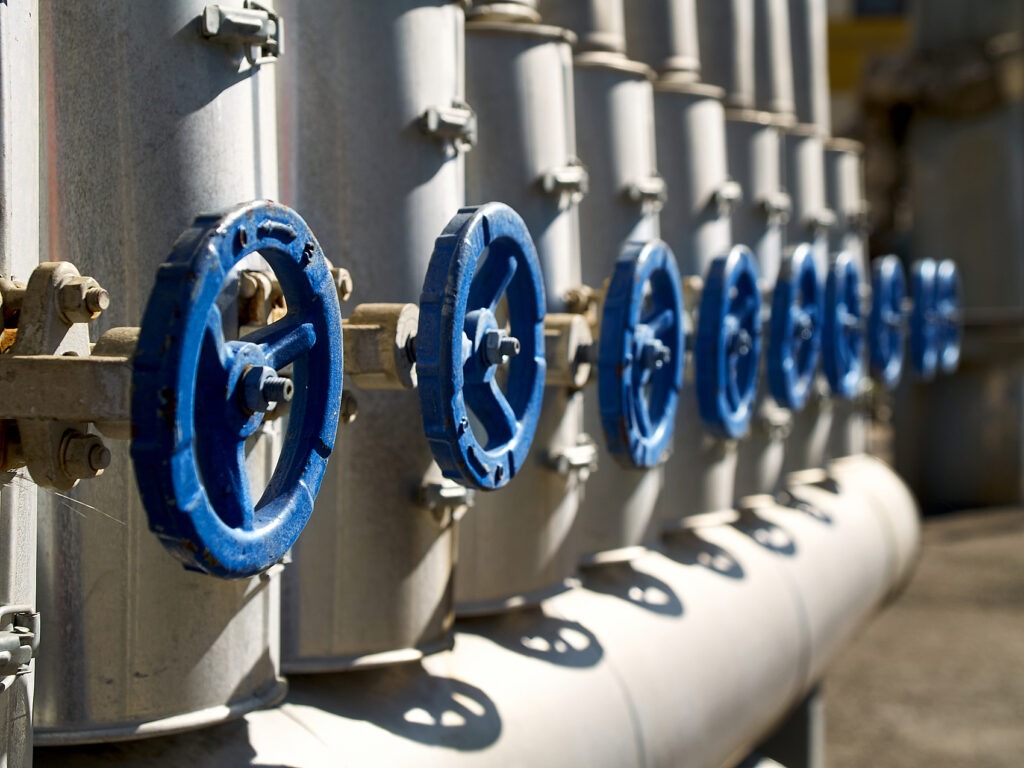
Handwheel: For manually operated control valves, a handwheel is a common fitting used to manually rotate the valve to regulate fluid flow or pressure.
Handle: Similar to a handwheel, a handle is an accessory used for manual operation, usually on small or lightweight valves.
Manual Operating Devices: For electric or pneumatic control valves, manual operating devices allow the valve to be operated manually in the event of a power or air source failure, ensuring system reliability.
Accessory Bracket: A bracket for mounting an accessory, such as a position feedback device or other instrumentation.
Position Indicator: Provides a visual indication of the position of the valve so that the operator can visualize the status of the valve.
Seal kits: Kits containing replacement seals and sealing material for maintaining and repairing valves to ensure their sealing performance.
Connectors: Accessories used to connect control valves to piping systems, such as flanges, threaded connectors, etc.
Heaters or insulating jackets: used to prevent the valve from freezing in cold environments or to maintain fluid temperature in hot environments.
Shields: Used to protect control valves from external environments such as corrosion, particulate matter, or inclement weather.
Fire shields: Provide additional fire protection for applications that require operation under fire conditions.
Piping fittings: Piping accessories, including elbows, tees, etc., used to connect the control valve to the piping system.
The selection of these fittings depends on the type of control valve, the application environment, and the function required. When installing and maintaining control valves, the correct selection and use of fittings is an important factor in ensuring the performance of the valve and the stability of system operation
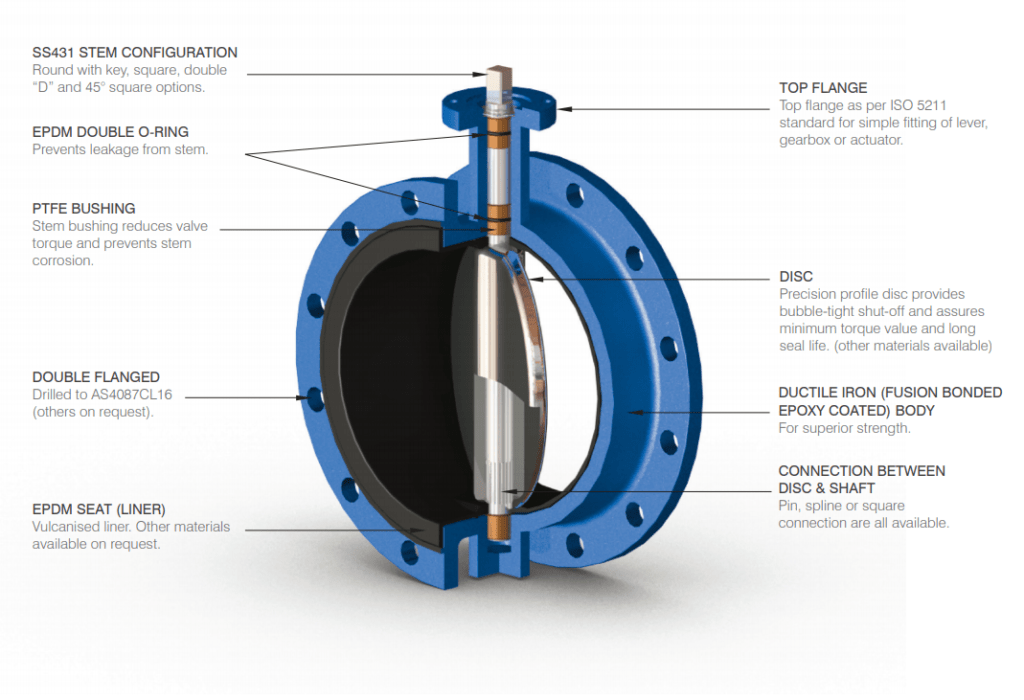
Typical applications of valves
control valve is the key part of the control circuit, is a key control element in the industrial process, which consists of pneumatic actuator, electric actuator or hydraulic actuator components and valves, used to regulate the flow or temperature of the fluid, or the upstream pressure and downstream pressure or liquid level. It is widely used in petroleum, chemical, pharmaceutical, textile, paper making, oil refining, oil and gas, iron and steel metallurgy and other industries.
Understand the most appropriate type of flow control valve for your application
Understanding the most appropriate type of flow control valve to choose is critical for industries. The market offers a wide range of flow control valves, some of which are called flow control valves because of their complex design and ability to automatically adjust to changes in pressure and temperature. The construction of these valves varies, but the common goal is to regulate the flow or pressure of a fluid based on signals from flow meters, sensors and transmitters. When selecting the right type of valve, the specific needs of the application need to be considered, including the industrial sector, the characteristics of the fluid, and the need for automatic regulation.
Basic Control Valve Terms and Explanations
There are some basic terms used in the field of control valves, and understanding these terms is essential to understanding and operating a control valve. The following are some common control valve terms and their explanations:
Valve body: the main part of the valve, including the passage through which the fluid passes. The design and shape of the valve body directly affects the performance and scope of application of the valve.
Valve flap: the moving part of the control valve, usually disc or cylindrical shape, used to regulate the passage or flow of fluid.
Seat: the part of the valve in contact with the valve flap, usually made of wear-resistant materials, to ensure the sealing performance of the valve when it is closed.
Actuator: A device used to control the position of a valve, which can be operated automatically or manually according to a signal. Common types of actuators include electric actuators, pneumatic actuators and hydraulic actuators.
Position Feedback: Device used to detect and feedback the position of the valve to help the actuator to achieve accurate position control.
Flow Characteristics: Properties that describe the relationship between flow and valve position when the valve is open. Common flow characteristics include equal percentage (EQ%), linear, fast open, etc.
Failure Position: The predetermined position taken by the valve when the control system fails, which can usually be open, closed or hold the current position.
Deadband: The minimum range in which the actual position of a control valve needs to change after receiving a signal. Deadband can lead to instability in the control system.
Valve Stroke: The length of a valve’s travel from closed to fully open. Adjustment of the valve stroke affects the change in fluid flow.
CLOSED LOOP CONTROL: The use of feedback in a control system to adjust the position of a valve in such a way as to maintain a desired flow or pressure.
Overall, there are many factors to consider when selecting and calculating control valves, and the above is not an exhaustive list. We will endeavor to keep this content up to date, but in the meantime, if you need specific formulae and sizing information, please feel free to download the resources we offer, details of which can be found on our downloads page.
Why more and more international valve brands choose DELCO for OEM service?
Founded in 2011, DELCO is a global leader in the industrial sector. Our main products include electric actuator valves, pneumatic actuator valves, automation actuators and solenoid valves. For nearly 20 years, we have utilized our products, engineering expertise and industrial automation solutions to solve countless industrial project problems for our customers, including food, beverage, chemical, water treatment, pharmaceutical, natural gas, oil and HVAC projects. We currently have five subsidiaries and more than 50 distributors around the world providing rapid response service.
All DELCO products undergo a 100% in-house design, engineering and manufacturing process led by highly skilled and experienced engineers using Italian and German technology to manufacture high quality, safe, reliable and value for money valves, actuators and solutions. Manufacturing standards can be demonstrated by the certifications obtained over the years.
And with the ISO 9001:2015 Quality Management System certification as well as many other certifications such as: SGS, RoHS, CNEX, TUV, CE, FDA. these certifications prove that DELCO adheres to the highest quality and safety standards worldwide when manufacturing its products.
How to get a quick quote for industrial valves?
If you have questions about valves or want to get a quote, please feel free to contact us, we will reply within 6 hours. Phone +86 159 8960 2972, WhatsApp +86 159 8960 2972 or email marketing [email protected].
DELCO’s quality, competitive prices and excellent service make it the best valve partner to help you grow your business. Customize your valves, we have no minimum order.
At DELCO, we understand the importance of customer satisfaction and strive to meet the unique needs of every client. As a reliable control valve supplier, we are committed to providing excellent customer service and high-quality products to ensure optimal performance and longevity. By choosing DELCO as your trusted control valve supplier, you can benefit from customized valve assemblies designed specifically to meet your requirements, enhancing efficiency and reducing downtime.
Furthermore, our competitive pricing on electronic pressure regulators enables you to offer top-notch solutions. As one of the leading control valve manufacturers, we take pride in delivering reliable valves that not only meet industry standards but also contribute to the overall profitability of your business. By partnering with DELCO, you can have peace of mind knowing that you are making a wise choice for the long-term success of your company.